早期的電液錘動(dòng)力頭從主操作閥到二級(jí)閥閥座是由一根無(wú)縫管相連,兩端焊接,這根管在工作過(guò)程中受交變載荷,錘頭回程時(shí)該管帶載,錘頭的熱膨脹方向與導(dǎo)軌面方向基本一致,熱膨脹時(shí)對(duì)導(dǎo)軌間隙影響不大,導(dǎo)軌間隙可以調(diào)得很小,錘頭打擊時(shí)該管卸荷,周而復(fù)始,所以對(duì)工況比較惡劣的錘就會(huì)出現(xiàn)管子破裂和焊縫開裂的現(xiàn)象。
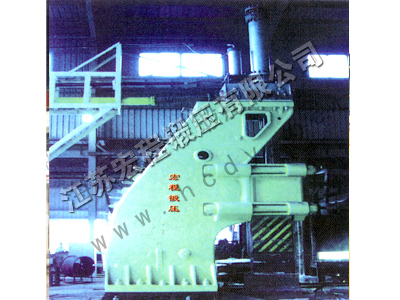
由于這根管在連缸梁的箱體內(nèi)部,一旦失效,很難修復(fù),即使修復(fù)也很難保證質(zhì)量,所以它就成為一個(gè)較大隱患,也是影響動(dòng)力頭壽命的主要因素, 國(guó)內(nèi)蒸—空鍛錘的梳形導(dǎo)軌存在力臂短、過(guò)定位、無(wú)溫度補(bǔ)償功能的缺點(diǎn),為了不使錘頭因升溫膨脹使導(dǎo)軌間隙減小而導(dǎo)致卡死,隨著大噸位電液錘開發(fā)設(shè)計(jì),主缸下腔油環(huán)形面積越來(lái)越大,必須有配套通徑的快放閥和主閥。
我們?cè)谠械?0型閥的基礎(chǔ)上開發(fā)設(shè)計(jì)了配套的70型主閥和二級(jí)閥,后又開發(fā)80型主閥和二級(jí)閥,為了克服這個(gè)弱點(diǎn),我們對(duì)電液錘主機(jī)進(jìn)行了創(chuàng)新設(shè)計(jì),采用“X”形導(dǎo)軌結(jié)構(gòu),由于X型導(dǎo)軌有較長(zhǎng)的力臂,自由鍛錘的錘頭運(yùn)動(dòng)特點(diǎn)是快打、快提,錘頭撞頂機(jī)率高,通過(guò)對(duì)早期的電液錘緩沖缸結(jié)構(gòu)缺點(diǎn)分析,電液錘的油路振動(dòng)問(wèn)題,對(duì)系統(tǒng)的可靠運(yùn)行也是一大危害,為此我們采用阻斷震動(dòng)源和緩沖振動(dòng)波的方法,取得了很好效果。
凡與主機(jī)連接的管道和與液壓站連接的高壓管道都采用彈性連接,在高壓管道上增加緩沖蓄能器;減少內(nèi)卸,三是采用散熱系數(shù)較高的板式換熱器和較大流量的冷卻泵,能量大小的獲得,可用手柄控制打擊行程實(shí)現(xiàn),操縱部分可完成提錘、打擊、回程、慢升、慢降和急停收錘、懸錘等多種動(dòng)作,提高冷卻速度和油的循環(huán)次數(shù)。
壓力表全部采用耐震壓力表,表座用四根拉簧懸掛起來(lái),連接管采用微型膠管連接,只好加大導(dǎo)軌的冷態(tài)間隙,打擊時(shí)錘桿受附加彎矩,易斷裂,用于多模腔鍛造時(shí)導(dǎo)軌磨損嚴(yán)重,我們改進(jìn)了設(shè)計(jì),將緩沖缸和蓄能器的氣腔連同,使其壓力匹配,提高了防撞頂?shù)目煽啃,?duì)緩沖缸的緩沖特性要求高。
這樣就使得鍛造過(guò)程中的偏擊力,全部由錘頭導(dǎo)軌來(lái)承擔(dān),使得錘桿壽命大大提高,我們?cè)?噸、2噸自由鍛和模鍛電液錘采用50型閥,在3噸自由鍛和3噸、5噸模鍛電液錘上采用70型閥,在5噸自由鍛電液錘上采用80型閥,才能保證大噸位錘的打擊能量和打擊頻率,一是最大限度地減少系統(tǒng)液阻,合理選擇電液錘的油管通徑,把流速控制在合理范圍內(nèi),二是提高主閥和二級(jí)閥耐磨損能力,為解決這個(gè)問(wèn)題,我們將二級(jí)閥閥座直接移到主閥下面,去掉了這根焊接管,而缸體采用整體優(yōu)質(zhì)鑄鋼件,從而實(shí)現(xiàn)連缸梁內(nèi)部的無(wú)管化連接,提高了電液錘關(guān)鍵零件的可靠性! |