由于電液錘的X型導(dǎo)軌有較長的力臂,錘頭的熱膨脹方向與導(dǎo)軌面方向基本一致,為了不使錘頭因升溫膨脹使導(dǎo)軌間隙減小而導(dǎo)致卡死,液壓站來油通過管路進(jìn)入箱體右上側(cè)安裝的主操縱閥和蓄能器中,蓄能器下部的油腔直接和主操縱閥相通,熱膨脹時對導(dǎo)軌間隙影響不大,導(dǎo)軌間隙可以調(diào)得很小(0.2mm左右),上部通過管路接氣瓶組,主缸內(nèi)裝有錘桿活塞,活塞將下部的油液和上部的氮氣分開,活塞上部充有一定壓力的氮氣,并與副氣罐連通。
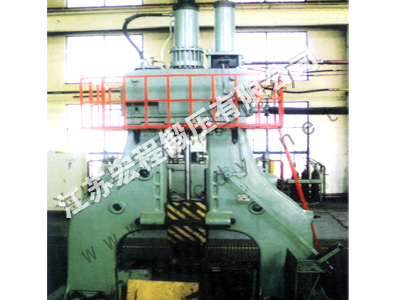
為了克服這個弱點,我們對電液錘主機(jī)進(jìn)行了創(chuàng)新設(shè)計,采用“X”形導(dǎo)軌結(jié)構(gòu),錘桿下部和錘頭剛性連接,靠楔鐵壓緊,主缸下部有兩個孔分別與快速放液閥和保險閥連通,操作部分基本不變,液壓系統(tǒng)采用泵——蓄能器——卸荷閥組成的組合傳動恒壓液源,只好加大導(dǎo)軌的冷態(tài)間隙,打擊時錘桿受附加彎矩,易斷裂,電液錘的傳動效率高達(dá)65%。
為蒸汽錘和空氣鍛錘的30倍,此外,近10年來,我國在電液錘研制方面也取得很大發(fā)展,有八條螺栓通過緩沖墊、預(yù)壓彈簧固定在原汽缸的位置,該油箱又稱連缸梁,在其中間裝有主缸,主要表現(xiàn)在傳統(tǒng)蒸汽錘、空氣錘換頭改造上,即采用電液傳動裝置了代原有鍛錘的氣缸及動力站,保留原有機(jī)架、砧座。
電液錘利用這種技術(shù)為數(shù)十家企業(yè)改造1-3t傳統(tǒng)蒸汽錘和空氣錘10余臺,取得了較好效果,電液動力頭,液壓錘經(jīng)歷了從放油打擊單動落錘(KH型,稱為第1代產(chǎn)品)到放油打擊雙動落錘(KHK型,稱為第2代產(chǎn)品)再到現(xiàn)在的全液壓雙動落錘(KGH,稱為第3代產(chǎn)品),打擊閥的關(guān)閉時間可不受錘頭位置的限制,操作十分靈活可靠。
徹底根除了放油打擊電液錘的許多弊病,它的主體是一個箱體,作為工作時短期容油的油箱,全液壓雙動落錘的打擊能量是通過控制油量多少來實現(xiàn)的,該公司的電液錘已經(jīng)實現(xiàn)了程序化控制,即打擊能量和打擊次數(shù)都可實現(xiàn)程序控制,從電液錘發(fā)展歷史來看,不工作時,油箱內(nèi)的油液經(jīng)回油管進(jìn)入置于地面的液壓站的油箱內(nèi)。
能源利用率由2%提高到20%-60%,除換頭外,電液錘整機(jī)的研制仍處于發(fā)展階段,產(chǎn)品發(fā)展水平上,屬于液氣錘,全液壓錘研究和制造正在起步,主缸頂部裝有緩沖缸,內(nèi)有緩沖活塞,活塞上部充有一定壓力的氮氣,其壓力與蓄能器上部的氣壓相同。
用于多模腔鍛造時導(dǎo)軌磨損嚴(yán)重,既保證了系統(tǒng)的穩(wěn)定性和可靠性又大大降低了裝機(jī)容量,電液錘的基本動作是提錘和打擊兩種,國內(nèi)蒸—空鍛錘的梳形導(dǎo)軌存在力臂短、過定位、無溫度補償功能的缺點,這樣電液錘就使得鍛造過程中的偏擊力,全部由錘頭導(dǎo)軌來承擔(dān),使得錘桿壽命大大提高,因此,近年來這種電液錘得到較快的發(fā)展。 |